A new generation of UV-curing silicones and epoxies are increasingly being used in automotive and electronics applications.
Every action in life involves a trade-off: The gaining of one benefit at the expense of another, to best meet the needs of the situation at hand. When the situation involves high-volume bonding, sealing or gasketing, manufacturers rely on UV-cure adhesives because they allow on-demand and quick curing (1 to 5 seconds after light exposure).
The trade-off, however, is that these adhesives (acrylic, silicone and epoxy) require a transparent substrate to properly bond, and they cost significantly more than adhesives that cure by other means. Nevertheless, countless manufacturers in many industries have happily made this trade-off for several decades. Many more companies will do so for the foreseeable future. The difference, however, is that engineers will be as likely to use a silicone or epoxy UV-cure adhesive, as one that’s acrylic-based.
“Although we’ve made UV-cure silicones for the last decade or so, in the last three years we’ve had to intensify our selling efforts to keep up with market demand,” notes Doug McKinzie, vice president of specialty products at Novagard Solutions. “Our UV-cure silicone sales have increased 50 percent the past few years. This will lessen some, but we still expect good growth for the next several years.”
Among the biggest users of UV-cure silicones are automotive OEMs, and Tier 1 and Tier 2 suppliers. One Tier 2 supplier uses Loctite SI 5031 sealant from Henkel Corp. to pot terminals in housings for electronic brake-control modules and tire-pressure sensors. The company also uses Loctite SI 5039 to form a UV-cured-in-place silicone gasket around the perimeter of each module. Bill Brown, manager of applications engineering for Henkel, says that both products contain a fluorescent dye to help verify adhesive presence during final inspection.
This subassembly is then sent to a Tier 1 supplier that inserts additional internal components and connects a PCB to the terminals. A cover is placed over the perimeter gasket to create an environmentally tight seal on the final assembly.
UV-cure epoxy adhesives are also frequently used for automotive and consumer electronics applications. One reason is that these adhesives, like silicones, are specifically formulated to match the wavelength of LED light sources (320 to 550 nanometers), so manufacturers get all of the benefits of LED lighting, such as long life, limited heat and flexible configurations. Another reason is the lower capital costs of UV curing, thereby making it easier for companies to trade up to this technology.
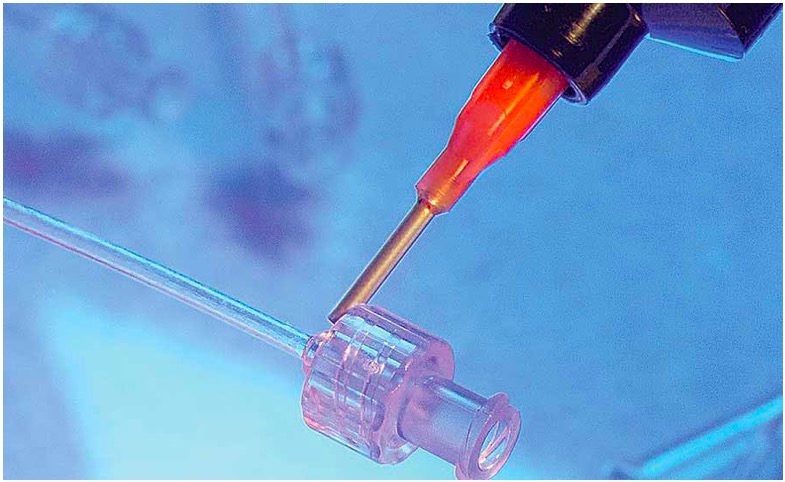
Post time: Aug-04-2024